Air Preheaters: Your Furnace’s Energy Saver
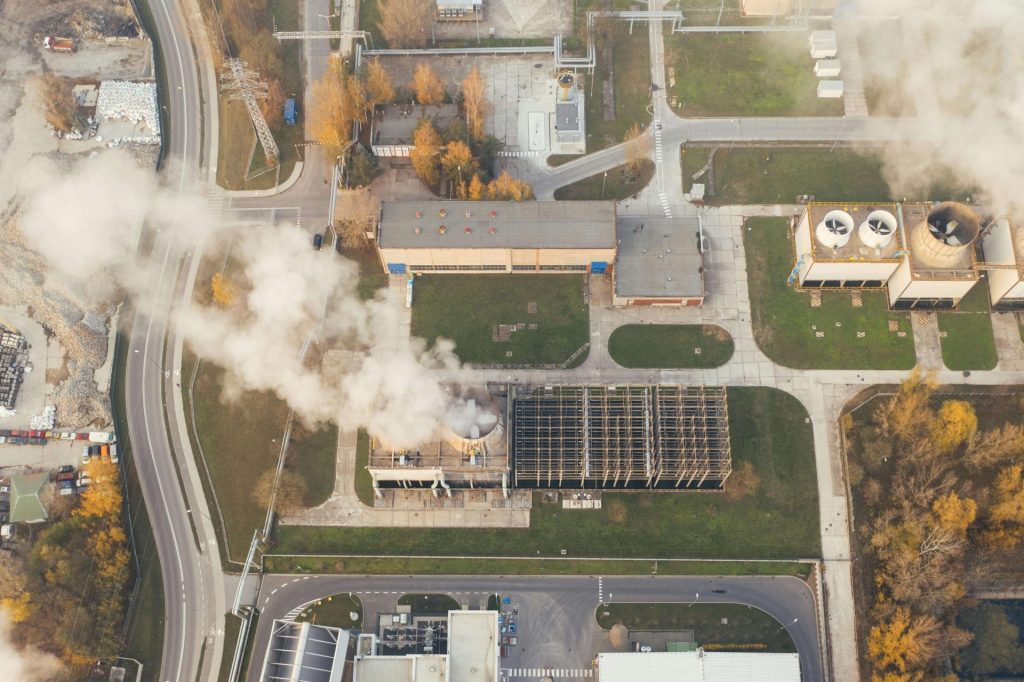
In industrial heating furnace systems, the air preheater is often called the "secondary developer of thermal energy." By recovering waste heat from flue gas to preheat combustion air, this seemingly simple heat exchange process can revolutionize the energy efficiency of entire furnace systems. This article explores the critical role of air preheaters in heating furnaces through three dimensions: principles, benefits, and optimization.
1. How Air Preheaters Work
The core task of an air preheater is to convert "waste heat → new thermal energy":
- Heat Recovery Process
- High-temperature flue gas (typically 300-600°C) flows through the preheater’s heat exchange surfaces.
- Heat transfers via metal tubes/regenerative materials to cold air (ambient → 200-400°C).
- Flue gas exits at reduced temperatures (120-200°C).
2. Four Core Benefits of Air Preheaters
- Energy Savings: Direct Economic Value
- Fuel Reduction: Preheating air by 100°C lowers fuel consumption by 4-7%.
- Case study: A petrochemical plant saved 1.2 million m³/year of natural gas after installing preheaters.
- Power Optimization: Reduced induced draft fan load (flue gas volume shrinks as temperature drops).
- Fuel Reduction: Preheating air by 100°C lowers fuel consumption by 4-7%.
- Emission Reduction: Essential for Green Production
- Lower flue gas temperatures cut thermal pollution (sensible heat loss reduced by 30%+).
- Improved combustion efficiency slashes CO emissions by 50-80%, supporting carbon neutrality goals.
- Equipment Protection: Extended System Lifespan
- Prevents low-temperature corrosion by maintaining flue gas temperatures above the acid dew point (typically >150°C).
- Stabilizes combustion to minimize thermal stress on furnace tubes.
- Process Optimization: Enhanced Product Quality
- Stabilizes furnace temperature fields (fluctuations reduced from ±25°C to ±8°C).
- Critical for industries like glass kilns, where temperature stability directly impacts product quality.
3. Operational Challenges & Solutions
- Common Issues
- Ash Deposition: Dust accumulation reduces efficiency by up to 30%.
- Low-Temperature Corrosion: SO₃ condensation forms sulfuric acid, corroding surfaces.
- Excessive Air Leakage: Rotary preheater leakage rates >10% negate energy savings.
- Advanced Solutions
- Intelligent Soot-Blowing Systems
- Acoustic cleaners: Non-contact cleaning for fragile components.
- Steam-blowing algorithms: Auto-adjust frequency based on pressure differentials.
- Anti-Corrosion Coatings
- Enamel coatings: Acid-resistant, lifespan >5 years.
- Fluoropolymer coatings: Low surface energy prevents ash buildup.
- Sealing Innovations
- Magnetic seals: Reduce rotary preheater leakage to <5%.
- Flexible seals: Compensate for thermal expansion.
- Intelligent Soot-Blowing Systems
4. Key Considerations for Selection & Maintenance
- Selection Principles
- Thermodynamic Matching: Size heat exchange area based on flue gas flow/temperature.
- Material Compatibility: Use ND steel or composites in acidic environments.
- Maintenance Accessibility: Reserve space for cleaning and inspections.
- Maintenance Best Practices
- Daily Checks: Monitor inlet/outlet temperature differentials (150-300°C normal range).
- Monthly Tasks:
- Test soot-blowing systems.
- Measure leakage rates (≤8% for rotary, ≤3% for tubular).
- Annual Overhaul:
- Measure corrosion rates (replace components if >0.2 mm/year).
- Recalibrate sealing systems.
5. Future Trends: Smart Preheating Systems
Next-gen air preheaters are evolving with:
- Digital Twins: Real-time thermal simulations to predict ash buildup.
- AI-Driven Optimization: Auto-adjust bypass dampers based on load changes.
- Hydrogen Fuel Adaptations: Material/structure upgrades for clean energy combustion.
Air preheaters are not just the "energy-saving heart" of heating furnaces but also "carbon reduction pioneers" for sustainable manufacturing. Through smart selection, maintenance, and upgrades, industries can unlock their full potential. If your furnace’s flue gas temperature exceeds 200°C, it’s time to reevaluate your preheater system!