Online Revamping: Where Tech Meets Green Growth.
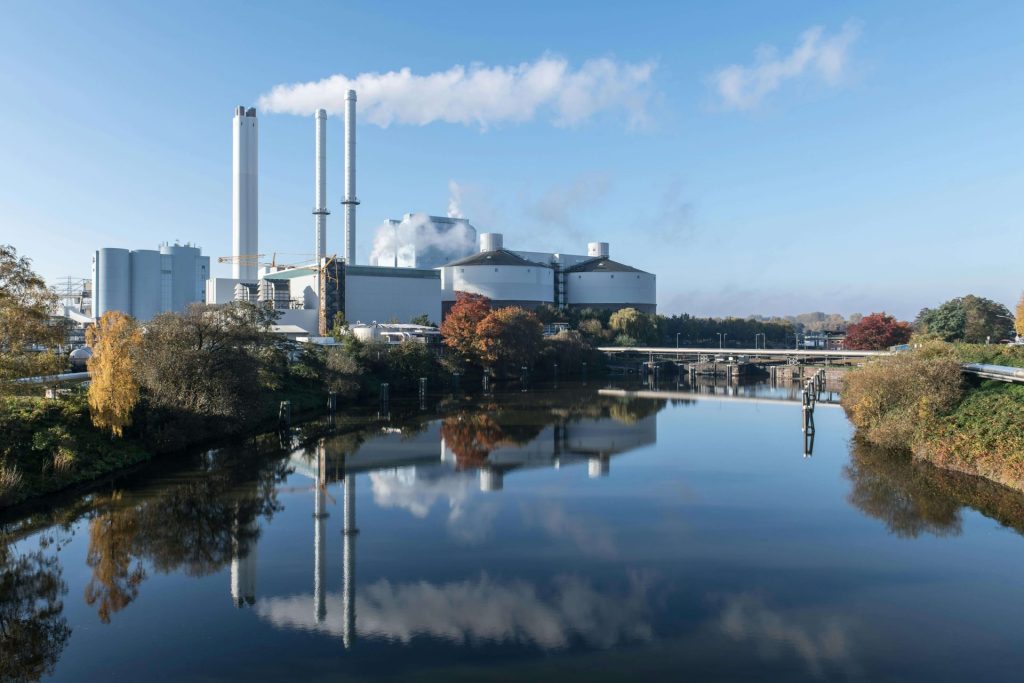
In refining, petrochemical, and other process industries, heating furnaces are core equipment, and their operational efficiency directly impacts energy consumption, carbon emissions, and economic performance. However, traditional petrochemical heating furnaces often face challenges such as low thermal efficiency, high pollutant emissions, and insufficient automation. Shutting down for conventional retrofitting incurs high costs and risks disrupting the supply chain. Thus, online revamping (non-stop retrofitting) has become a preferred choice for many enterprises. This blog explores the key aspects of online revamping for petrochemical heating furnaces, covering technical pathways, implementation challenges, and industry value.
I. Why Choose Online Revamping?
- Economic Benefits: Traditional retrofitting requires weeks or months of shutdowns, leading to significant losses. Online revamping enables continuous production through phased construction and modular replacement, minimizing downtime costs.
- Environmental Compliance: Stricter global emission regulations (e.g., NOx, CO₂ limits) demand rapid integration of technologies like low-NOx burners and waste heat recovery systems. Online revamping helps meet these standards without delays.
- Smart Upgrade Needs: Manual monitoring of traditional furnaces often results in efficiency fluctuations. Online revamping allows embedding smart control systems (e.g., AI-optimized combustion, digital twin monitoring) for precise temperature control and energy management.
II. Core Technical Pathways for Online Revamping
- Combustion System Optimization
- Low-NOx Burners: Reduce NOx emissions by 30%-50% via staged combustion or flue gas recirculation (FGR).
- Fuel Flexibility: Enable multi-fuel compatibility (e.g., hydrogen blending) for enhanced energy adaptability.
- Deep Waste Heat Recovery
- Install high-efficiency heat exchangers in existing flues to preheat air or process media, boosting thermal efficiency by 5%-10%.
- Apply heat pipe technology to mitigate high-temperature corrosion and extend equipment lifespan.
- Smart Control Systems
- Deploy real-time sensors (e.g., infrared thermography, gas analyzers) to monitor furnace temperature and combustion efficiency.
- Use AI algorithms to dynamically adjust air-fuel ratios, optimizing combustion across all operating conditions.
- Structural Reinforcement & Maintenance Optimization
- Apply high-temperature ceramic coatings to critical areas to reduce coking and corrosion.
- Design modular maintenance access to simplify future repairs.
III. Challenges & Solutions in Online Revamping
- Safety Risks During Construction
- Challenge: High-temperature, pressurized environments pose hazards.
- Solution: Use non-sparking mechanical connections and remote welding robots to minimize worker exposure.
- Balancing Retrofitting and Production
- Challenge: Local modifications may disrupt temperature distribution.
- Solution: Conduct CFD simulations to predict impacts and adjust loads incrementally.
- Quality Assurance
- Challenge: Hidden defects due to limited shutdown inspections.
- Solution: Implement non-destructive testing (e.g., industrial endoscopes, ultrasonic thickness gauges).
IV. Case Study: Atmospheric Furnace Revamping in a Refinery
A refinery upgraded an atmospheric heating furnace online, focusing on burners and control systems:
- Results: Thermal efficiency increased from 82% to 90%, NOx emissions dropped below 50mg/m³, and annual fuel savings exceeded $110,000.
- Timeline: Completed in 15 days without disrupting downstream operations.
V. Industry Outlook
As global "dual-carbon" goals advance, green and smart retrofitting of petrochemical heating furnaces will become imperative. Future online revamping will integrate:
- Digital Twins: Virtual commissioning and real-time simulation to shorten timelines.
- Hydrogen Readiness: Structural designs for 100% hydrogen combustion.
- Carbon Capture Integration: Pre-installed interfaces for future carbon capture systems.
Online revamping of petrochemical heating furnaces is not merely a technical upgrade but a strategic response to cost pressures, environmental mandates, and market competition. By leveraging innovative technologies and meticulous planning, enterprises can achieve energy efficiency leaps and sustainable growth without shutdowns or load reductions. For the industry, this marks a critical step toward high-quality development.
Contact our technical team for customized revamping solutions!