Low-NOx Burners: The Science of Cleaner Industrial Flames
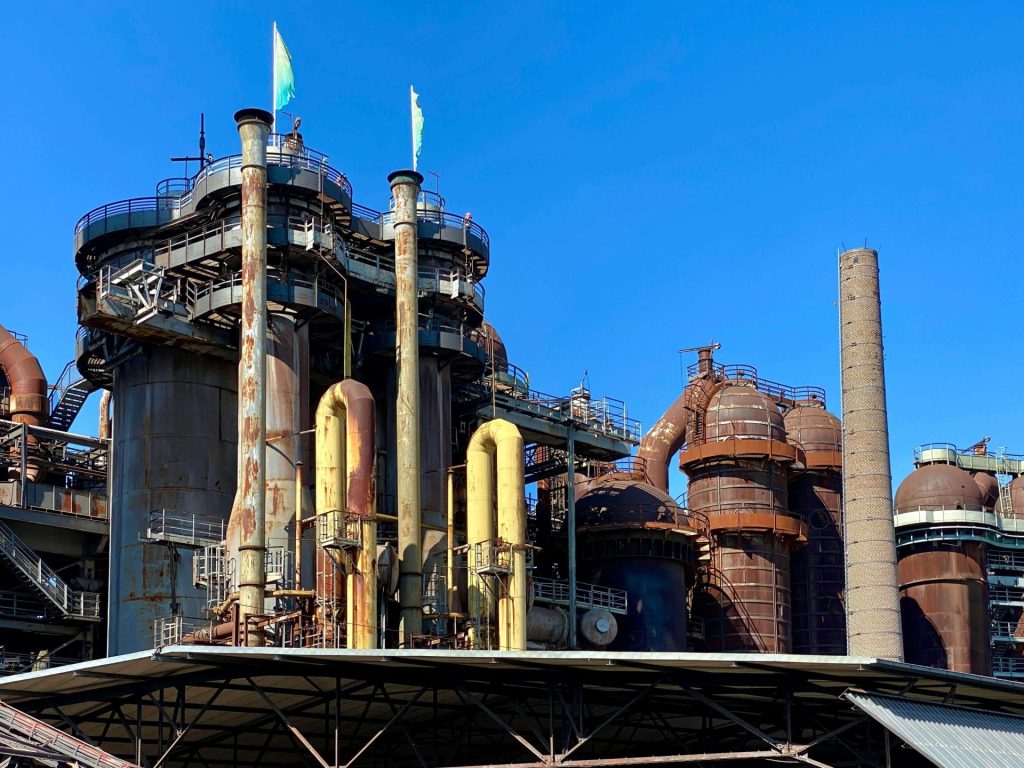
Under the "Dual Carbon" goals, green transformation in industrial sectors has become urgent. As a major source of atmospheric pollutant NOx (nitrogen oxides), traditional industrial combustion equipment faces severe challenges. Low-NOx burners, with their revolutionary technical principles, have emerged as the "master key" to solving this problem. This article delves into how low-NOx burners achieve high-efficiency emission reduction through scientific methods, empowering industrial boilers, gas turbines, and other equipment with "green DNA."
I. The NOx Generation Dilemma: Why Are Traditional Burners Eco-Unfriendly?
During high-temperature combustion, nitrogen (N₂) and oxygen (O₂) in the air undergo chain reactions in the flame core zone (typically exceeding 1400°C), generating NOx. Traditional burners, prioritizing complete combustion, often mix fuel with excess air, leading to high flame temperatures and localized oxygen surplus, which drastically increases NOx emissions. Statistics show that uncontrolled gas boilers can emit 200-300 mg/m³ of NOx, far exceeding environmental standards.
II. Four Core Technologies of Low-NOx Burners
Low-NOx burners tackle NOx generation at its source by "controlling flame temperature" and "optimizing reaction environments" simultaneously. Their core technologies fall into four categories:
- Staged Combustion: Simmering the Flame
- Fuel Staging: Fuel is injected in multiple streams. The first stream burns rapidly in an oxygen-rich zone, while the second stream delays combustion in an oxygen-lean zone, reducing overall combustion intensity.
- Air Staging: Combustion air is injected in phases. Initial oxygen supply is restricted to suppress high-temperature zones; remaining air is supplemented later to ensure complete fuel burnout.
- Effect: Peak flame temperature drops by 100-200°C, reducing NOx generation by 30%-50%.
- Flue Gas Recirculation (FGR): The "Second Life" of Exhaust
- Recirculating low-temperature flue gas (150-300°C) back into the combustion zone dilutes oxygen concentration and absorbs heat, creating a "mild" combustion environment.
- Key: Precise control of recirculation volume (typically 10%-30% of total flow) via induced draft fans to avoid combustion instability or efficiency loss.
- Premixed Combustion: The "Cool Flame" Alchemy
- Fuel and air are thoroughly premixed before entering the combustion chamber, forming a homogeneous gas that eliminates localized hot spots.
- Advantage: Short, uniform blue flames with temperatures lower than traditional diffusion flames, reducing NOx emissions to below 30 mg/m³.
- Smart Control Systems: The Burner’s "AI Brain"
- Integrated oxygen sensors, temperature detectors, and adaptive algorithms adjust air-fuel ratios and staging in real time.
- Case Study: A gas boiler equipped with smart controls reduced NOx emission fluctuations from ±15% to ±3% while boosting thermal efficiency by 5%.
III. Applications and Challenges of Low-NOx Burners
- Industrial Boilers: Widely used in pharmaceuticals, food processing, etc., achieving NOx emissions below 50 mg/m³.
- Gas Turbines: Utilizing lean premix technology, they balance high efficiency with ultra-low emissions, becoming mainstream in power generation.
- Challenge: Combustion instability at low loads requires optimization via porous media stabilization.
IV. Future Trends: Hydrogen Adaptation and Carbon-Neutral Combustion
With the rise of zero-carbon fuels like hydrogen, next-gen low-NOx burners are exploring hydrogen-natural gas hybrid combustion. Adjusting hydrogen ratios could further slash carbon emissions. Additionally, disruptive technologies like Chemical Looping Combustion (CLC) use metal oxide oxygen carriers to isolate nitrogen entirely, promising "zero NOx emissions."
Low-NOx burners are not just a compliance-driven solution but a milestone in industrial combustion’s transition from "energy-intensive" to "carbon-precise." As materials science and digital technologies converge, this "flame purification revolution" will continue empowering the battle for blue skies.