Industrial Furnace Maintenance: Boosting Efficiency & Longevity
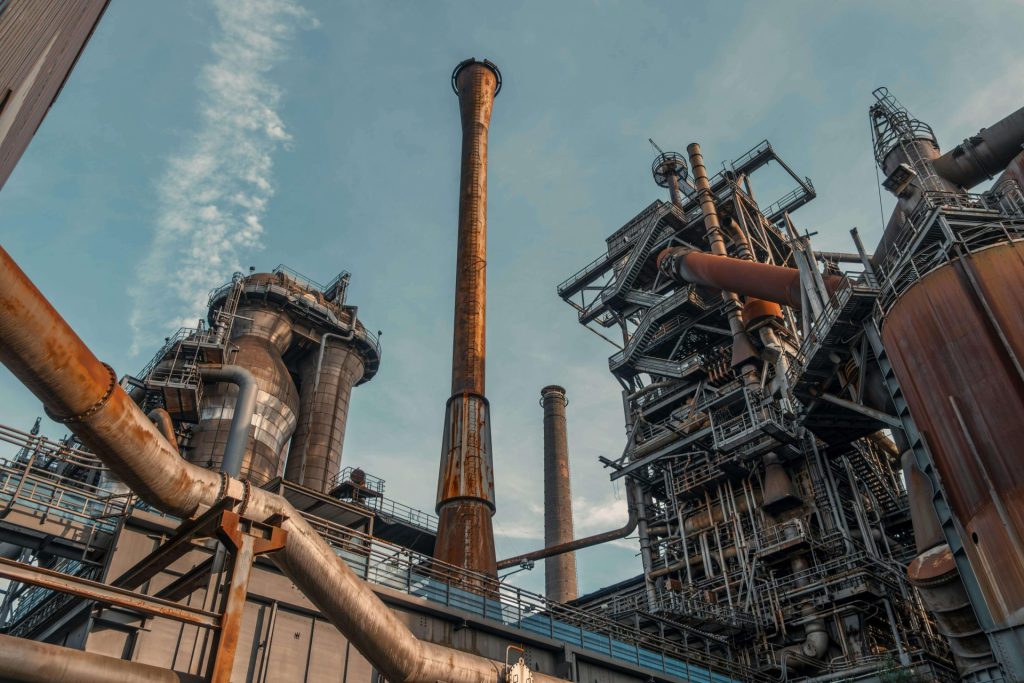
Industrial heating furnaces, serving as the "core equipment" in industries such as metallurgy, chemicals, ceramics, and glass, are critical for material heating, smelting, heat treatment, and other essential processes. However, harsh operating conditions—including high temperatures, corrosion, and prolonged operation—make them prone to high failure rates and energy consumption. Scientific and systematic maintenance not only reduces downtime risks and extends equipment lifespan but also significantly enhances energy efficiency, lowering operational costs for enterprises. This article delves into the core principles and practical techniques for industrial heating furnace maintenance.
I. The Necessity of Maintenance: Why It Can’t Be Ignored?
- Safety First: Furnace interiors can reach temperatures exceeding 1,000°C. Issues like gas leaks, refractory material failure, or control system malfunctions may lead to explosions or fires. Regular maintenance is the cornerstone of preventing catastrophic failures.
- Energy Savings: Problems such as ash buildup, coking, and insulation degradation reduce thermal efficiency and increase fuel consumption. Studies show that well-maintained furnaces can reduce energy use by 10–20%.
- Extended Equipment Lifespan: Corrosion, thermal oxidation, and mechanical wear gradually degrade furnace structures. Preventive maintenance can extend equipment life by over 30%.
- Ensuring Production Continuity: Unexpected failures can halt entire production lines, resulting in significant losses. Scheduled maintenance minimizes unplanned downtime and enhances operational stability.
II. Core Maintenance Strategies
- Daily Inspections and Documentation
- Visual Checks: Inspect the furnace shell for deformations, cracks, or localized overheating (using infrared thermometers).
- Combustion System Checks: Verify gas/fuel pipelines for leaks, ensure burner flames are stable and uniform, and watch for backfires or flameouts.
- Instrument Monitoring: Track real-time parameters like furnace temperature, pressure, and flue gas oxygen content; investigate anomalies promptly.
- Data Logging: Maintain maintenance records to analyze trends and predict potential failures.
- Scheduled Shutdown Maintenance
- Refractory Material Care: Inspect furnace walls and roofs for cracks or spalling in bricks or castables, especially in high-temperature zones. Repair or replace damaged sections.
- Heat Exchanger Cleaning: Remove ash and coking from regenerators, waste heat boilers, etc., using high-pressure water jets or mechanical scraping to restore efficiency.
- Burner Calibration: Adjust air-fuel ratios to ensure complete combustion (flue gas CO levels <50 ppm), minimizing waste and emissions.
- Mechanical Component Lubrication: Apply high-temperature grease to door mechanisms, conveyor chains, and other moving parts to reduce wear.
- Critical System-Specific Maintenance
- Control System Upgrades: Calibrate temperature sensors and pressure transmitters, optimize PLC programs for precise heating curves, and prevent over/under-heating.
- Waste Heat Recovery Optimization: Inspect seals on waste heat boilers and heat pipes, remove internal pipe scaling, and maximize heat recovery efficiency.
- Emergency System Testing: Simulate power outages or overtemperature scenarios to validate responses from safety valves, emergency shutoffs, and cooling systems.
III. Smart Maintenance with New Technologies
- IoT and Predictive Maintenance: Deploy wireless sensors to monitor furnace vibrations, temperature distribution, and more. Use AI algorithms to predict refractory lifespan or burner failures, enabling proactive repairs.
- Infrared Thermal Imaging: Scan furnace exteriors with thermal cameras to pinpoint insulation defects or internal refractory damage without disassembly.
- Advanced Materials: Adopt nano-coated refractories, ceramic fiber modules, and other high-performance materials to improve thermal resistance and reduce maintenance frequency.
IV. Developing a Scientific Maintenance Plan
- Priority-Based Management: Classify furnaces as A/B/C tiers, with critical units inspected daily and others weekly/monthly.
- Cycle Planning: Schedule annual overhauls, quarterly repairs, and monthly checks to align with production cycles.
- Hybrid Approach: Outsource complex tasks like refractory installation to specialists, while in-house teams handle routine upkeep.
Industrial furnace maintenance is far more than “cleaning and fixing”—it’s a systematic integration of technology, management, and innovation. By standardizing procedures, adopting smart tools, and training dedicated teams, enterprises can mitigate risks and achieve greener, more efficient production under carbon neutrality goals. Remember: Every investment in preventive maintenance translates to long-term competitiveness and sustainable returns.