Heating Furnace Coking Treatment Guide
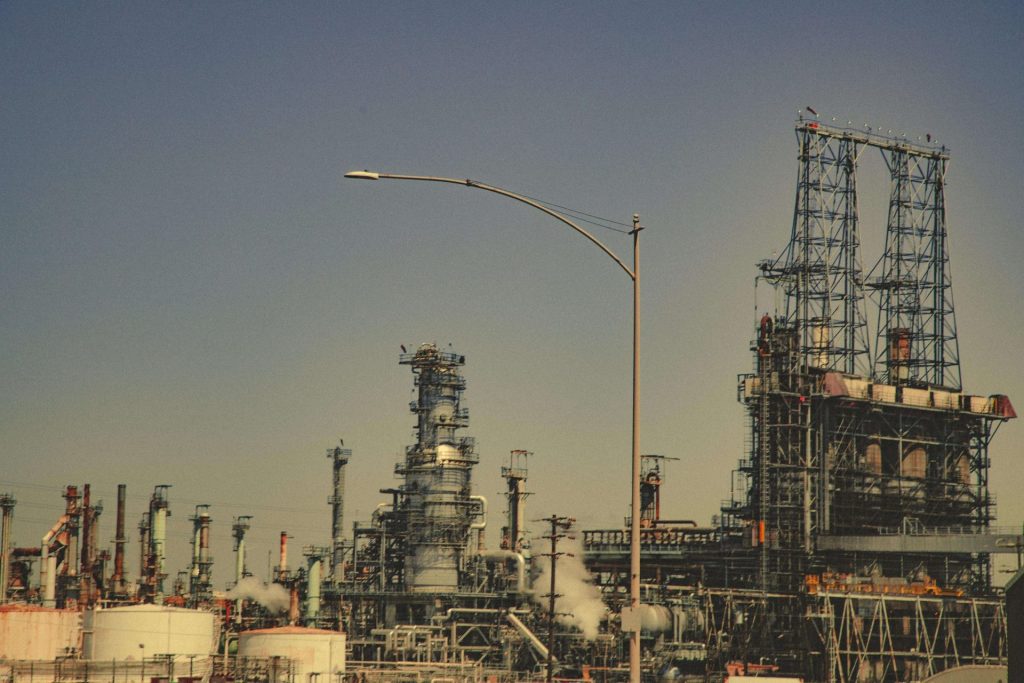
Coking inside heating furnaces is a common problem that affects equipment thermal efficiency, safe operation, and service life. This article systematically introduces the causes of coking, identification methods, and effective treatment measures.
I. Analysis of Coking Causes
- Fuel Factors
- High asphaltene and resin content in heavy fuel oil
- Excessive sulfur content in fuel
- Incomplete combustion due to poor fuel atomization
- Operational Factors
- Long-term low-load operation
- Improper air excess coefficient
- Uneven temperature distribution in the furnace
- Equipment Factors
- Burner design flaws
- High surface roughness of furnace tubes
- Excessive heat transfer surface temperature
II. Coking Identification Methods
- Operating Parameter Monitoring
- Abnormal increase in flue gas temperature (>15% above design value)
- Uneven surface temperature distribution of furnace tubes
- Significant increase in system pressure drop
- Visual Inspection
- Checking tube surfaces through inspection ports
- Endoscopic examination after shutdown
- Coking characteristics: Black, hard deposits, typically 1-10mm thick
- Laboratory Analysis
- Sampling for component analysis
- Measuring softening point of coke deposits
- Elemental analysis (C/H ratio, sulfur content, etc.)
III. Mechanical Decoking Methods
- Manual Decoking
- Applicable scenarios: Localized coking, accessible areas
- Tools: Specialized decoking shovels, wire brushes
- Precautions: Avoid damaging tube base material
- High-Pressure Water Jet Cleaning
- Pressure range: 70-150MPa
- Nozzle selection: Rotating multi-orifice nozzles
- Advantages: High efficiency, >95% decoking rate
- Sandblasting Treatment
- Abrasive selection: Steel shot, quartz sand, or walnut shells
- Particle size: 0.2-1.0mm
- Applicability: Stubborn coking with wear-resistant tubes
IV. Chemical Decoking Technologies
- Online Chemical Cleaning
- Cleaning agent: Specialized decoking agent (containing surfactants, dispersants)
- Concentration: 3-8%
- Temperature: 60-80°C
- Circulation time: 12-24 hours
- Offline Soak Cleaning
- Applicability: Severe coking cases
- Example formulation:
- 10% NaOH + 5% Na₃PO₄ + 1% surfactant
- Temperature 90-95°C, soak for 48 hours
- Ultrasonic-Assisted Cleaning
- Frequency: 20-40kHz
- Power density: 0.5-1.5W/cm²
- Enhanced effectiveness when combined with specialized cleaning agents
V. Coking Prevention Measures
- Fuel Optimization
- Control fuel viscosity (recommended 180-380cSt)
- Add anti-coking additives (0.1-0.3%)
- Regular fuel quality analysis
- Operational Optimization
- Maintain proper load (recommended 60-100% design load)
- Optimize air/fuel ratio (excess air coefficient 1.1-1.3)
- Regular soot blowing (steam or acoustic)
- Equipment Improvements
- Apply surface treatment technologies (aluminizing, ceramic coating)
- Improve burner design
- Install online monitoring systems
VI. Safety Precautions
- Complete energy isolation required before decoking
- Confined space work requires permits
- Personal protection during chemical cleaning
- Waste liquid disposal must comply with environmental regulations
VII. Performance Evaluation Standards
- Thermal efficiency restored to >95% of design value
- Furnace tube surface temperature difference <15°C
- Flue gas temperature reduced to design range
- System pressure drop reduced by >20%
Through these comprehensive measures, coking issues in heating furnaces can be effectively addressed. It is recommended to establish preventive maintenance plans, regularly inspect furnace tube conditions, and control coking problems at early stages to ensure long-term efficient and stable operation of heating furnaces.