Coke Oven: The “Black Heart” of the Steel Industry
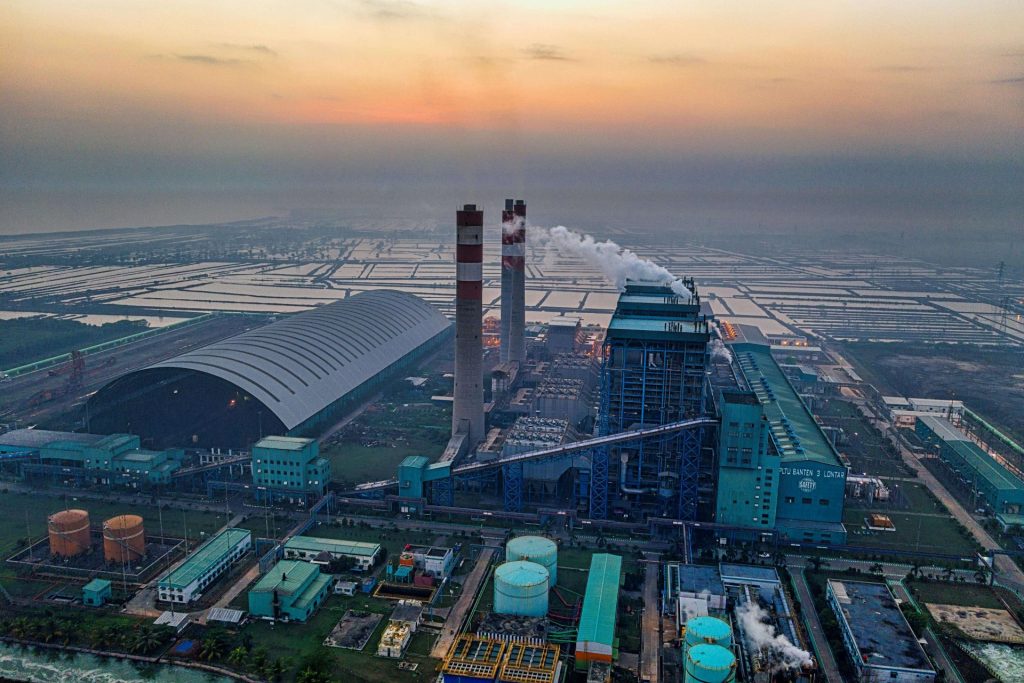
In heavy industries such as steelmaking and chemical production, there exists a piece of equipment known as the "black heart"—it transforms coal into coke, coal gas, and chemical raw materials through high temperatures, fueling the vast demands of modern industry. This critical device is the coke oven. In this blog, we’ll explore how coke ovens work, their core structure, and their pivotal role in industrial processes.
1. What Is a Coke Oven?
A coke oven is an industrial apparatus designed for the high-temperature dry distillation of coal (heating in the absence of air). Its primary function is to convert coal into metallurgical coke, while co-producing coke oven gas, coal tar, and other chemical byproducts. Coke serves as the "skeletal fuel" in blast furnaces for steelmaking, and coke oven gas is a valuable resource for clean energy and chemical synthesis. As such, coke ovens are central to integrated steel plants and coal-chemical industry chains.
2. Core Structure of a Coke Oven
A coke oven typically consists of alternating carbonization chambers and combustion chambers, built with high-temperature-resistant materials. Key components include:
- Furnace Structure
- Carbonization Chamber: The main space for coal dry distillation, constructed from refractory bricks capable of withstanding temperatures exceeding 1,200°C.
- Combustion Chamber: Located on either side of the carbonization chamber, it generates heat by burning gas or natural gas.
- Regenerator: Recovers waste heat to preheat air or gas entering the combustion chamber, improving energy efficiency.
- Heating System
- High temperatures are generated by burning gas or coke oven gas, with heat transferred indirectly through the chamber walls to the coal inside.
- Auxiliary Systems
- Coal Charging Car: Loads crushed coal into the carbonization chamber.
- Coke Pusher: Extracts finished coke from the chamber after distillation.
- Waste Gas Treatment System: Purifies harmful gases (e.g., hydrogen sulfide, benzene) produced during coking.
3. How Does a Coke Oven Work?
The coking process involves the thermal decomposition of coal, divided into three stages:
- Coal Loading and Sealing
- Crushed coking coal (with specific blending ratios) is loaded into the carbonization chamber, and the chamber is sealed to prevent oxygen exposure.
- High-Temperature Dry Distillation
- The combustion chamber heats up to 1,100–1,300°C, transferring heat through the walls to the coal.
- Under high temperatures, coal decomposes into solid coke (70–75%), gaseous coke oven gas (15–20%), and liquid coal tar (3–5%).
- Cooling and Coke Removal
- After distillation, the coke is cooled via water quenching or dry quenching (recovering waste heat) and then pushed out by the coke pusher.
- Coke oven gas is purified for use as industrial fuel or chemical extraction (e.g., benzene, ammonia).
4. Types of Coke Ovens
Coke ovens are categorized based on design and process differences:
- Top-Charging Coke Oven
- Coal is loaded from the top, producing high-quality coke. Ideal for large-scale production but requires significant investment.
- Stamp-Charging Coke Oven (Side-Charging)
- Pre-molded coal cakes are loaded from the side, allowing the use of lower-quality coal. Offers flexibility and is common in small-to-medium plants.
- Heat-Recovery Coke Oven
- Recovers waste heat for power generation, enhancing environmental performance, though the coke produced has lower strength.
5. Applications and Value of Coke Ovens
- Steel Industry
- Coke acts as a structural fuel in blast furnaces, facilitating iron ore reduction and maintaining gas permeability.
- Chemical Industry
- Coke oven gas yields hydrogen and methane, while coal tar is refined into benzene, phenol, asphalt, and other high-value products.
- Urban Gas and Power Generation
- Purified coke oven gas serves as municipal fuel or electricity generation feedstock.
6. Environmental Challenges and Innovations
While indispensable, coke ovens face environmental issues:
- Pollution: Emissions contain sulfides and nitrogen oxides; wastewater includes phenols and cyanides; solid waste (coke dust, slag) requires proper disposal.
- Technological Advancements:
- Cleaner Production: Adopts dry quenching, desulfurization, and denitrification.
- Waste Heat Recovery: Uses exhaust heat for power generation.
- Smart Control: AI optimizes combustion efficiency and reduces emissions.
- Hydrogen Energy: Explores hydrogen as a partial substitute for coke in blast furnaces.
7. Future Outlook
As the world advances toward dual carbon goals (carbon peaking and neutrality), the coke oven industry is transitioning toward greener, more efficient practices. Future coke ovens may evolve into clean energy hubs integrated with hydrogen and carbon capture (CCUS). Despite challenges, this "black heart" will continue powering industrial civilization.