Controlling CO and NOx Emissions in Petrochemical Burners: Key Strategies
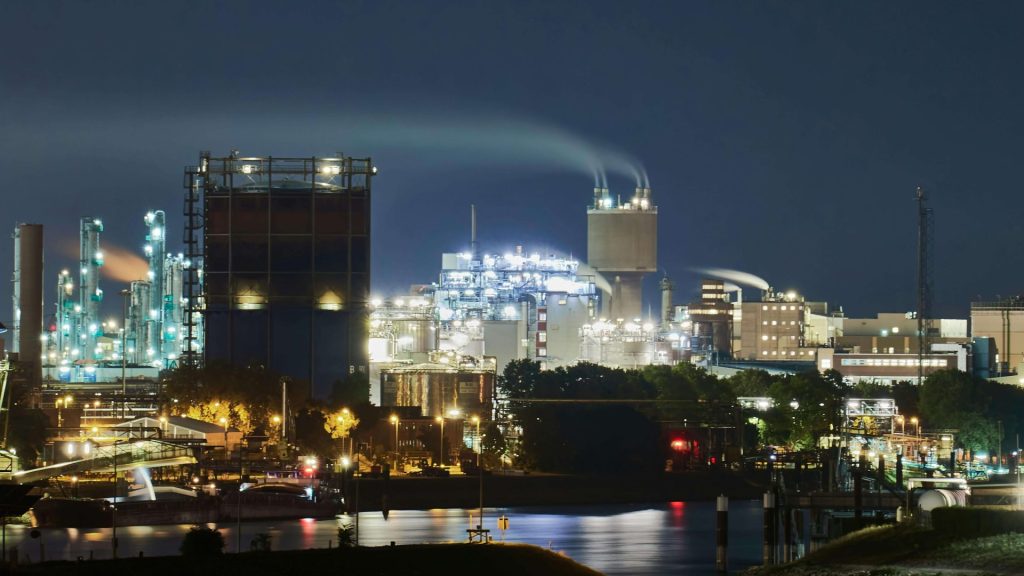
In the petrochemical industry, industrial burners are indispensable core equipment for production processes. However, emissions of CO (carbon monoxide) and NOx (nitrogen oxides) generated during combustion have long posed challenges for environmental governance. As global environmental regulations tighten, petrochemical companies urgently need to adopt technological upgrades to achieve efficient and clean combustion. This article explores mainstream CO and NOx control technologies and their practical applications in the industry.
1. Mechanisms of CO and NOx Formation
Before devising control strategies, it is critical to understand the generation mechanisms of these pollutants:
- CO: Primarily produced by incomplete fuel combustion, often due to imbalanced air-fuel ratios, insufficient oxygen, or poor mixing.
- NOx: Classified into thermal NOx (from N₂ and O₂ reactions at high temperatures), fuel NOx (oxidation of nitrogen compounds in fuel), and prompt NOx (reactions between hydrocarbons and nitrogen). Petrochemical burners mainly generate thermal NOx.
2. Combustion Process Optimization: Core Strategies for Source Reduction
- Low-NOx Burners (LNB) Technology
- By redesigning burner structures (e.g., multi-stage swirl designs, premixed combustion chambers), peak flame temperatures are reduced, and high-temperature residence time is shortened, effectively suppressing thermal NOx formation. For example, staged combustion (air staging or fuel staging) can reduce NOx emissions by 30%-50%.
- Precision Air-Fuel Ratio Control
- Real-time monitoring of oxygen levels using sensors and intelligent control systems (e.g., DCS, PLC) dynamically adjusts fuel and air ratios to ensure complete combustion (minimizing CO) while avoiding excess air that elevates NOx.
- Flue Gas Recirculation (FGR)
- Recirculating a portion of low-temperature flue gas into the combustion zone dilutes oxygen concentration and lowers combustion temperatures. Studies show FGR can reduce NOx emissions by up to 60%, though it requires stable combustion conditions.
3. Post-Combustion Treatment: Synergistic Auxiliary Technologies
- Selective Catalytic Reduction (SCR)
- Ammonia or urea is injected into flue gas, and catalysts (e.g., V₂O₅-WO₃/TiO₂) convert NOx into N₂ and H₂O at 300–400°C. SCR achieves over 90% denitrification efficiency but requires careful management of ammonia slip.
- Selective Non-Catalytic Reduction (SNCR)
- Reductants are injected into high-temperature zones (900–1100°C), suitable for small-to-medium burners. SNCR offers lower costs but efficiencies of only 30–70%.
- CO Oxidation Methods
- Catalytic oxidation units (e.g., Pt/Pd catalysts) convert CO to CO₂, often integrated with NOx treatment systems.
4. Innovative Technologies and Future Trends
- Hydrogen Co-Firing
- Blending hydrogen into fuels leverages its high diffusivity and clean combustion properties to reduce carbon-based emissions (including CO) and lower flame temperatures. Companies like Shell have validated this approach in pilot projects.
- Digital Twins and AI Optimization
- Digital models of burners combined with machine learning algorithms predict optimal operating parameters for dynamic emission control. For instance, BP reduced NOx emissions by 20% at a refinery using AI-driven adjustments.
- Ultra-Low-NOx Combustion Materials
- Advanced materials like high-temperature-resistant ceramic fibers optimize thermal distribution in burners, further inhibiting NOx formation.
5. Challenges and Balancing Act
- Cost vs. Environmental Benefits: High costs of SCR and other post-treatment technologies require companies to weigh investments against regulatory compliance.
- Multi-Pollutant Synergy: Reducing NOx must not trigger CO rebound, necessitating precise combustion parameter management.
- Fuel Flexibility: Petrochemical fuels vary widely (e.g., natural gas, heavy oil, refinery gas), demanding adaptable combustion technologies.
Emission reduction in petrochemical industrial burners hinges on an integrated revolution spanning combustion chemistry to smart controls. By adopting a multidimensional strategy—"source control + post-treatment + digitalization"—companies can meet regulatory standards while boosting energy efficiency and competitiveness. Looking ahead, the adoption of low-carbon fuels and zero-carbon technologies may drive a more profound green transformation of these systems.
Food for Thought: Under the "dual carbon" goals (carbon peaking and carbon neutrality), how can CO/NOx control synergize with carbon capture technologies to form integrated solutions? This may well be the next frontier for innovation.