Burners: Core of Efficient Crude Processing
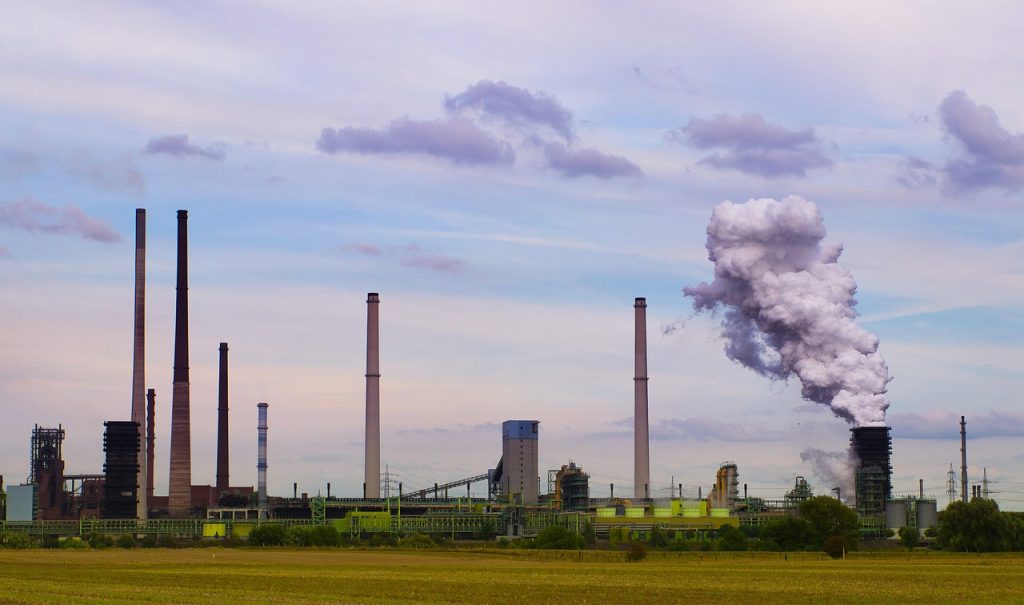
In the petroleum refining industry, the atmospheric and vacuum distillation furnace is a core facility for crude oil processing. Within this system, the burner acts as the furnace’s "thermal heart," directly determining the efficiency, energy consumption, and environmental performance of the entire unit. If the distillation furnace is the "fractionation engine" of a refinery, the burner is the "power source" driving this engine. This article delves into the pivotal role of burners and their indispensable value in ensuring the efficient operation of atmospheric and vacuum distillation furnaces.
I. The Thermal Energy Hub of Distillation Furnaces
The primary task of an atmospheric and vacuum distillation furnace is to heat crude oil to high temperatures, enabling its separation into oil products with varying boiling points. However, the efficiency of this process hinges entirely on the burner’s precise energy delivery:
- Heating Requirements: The atmospheric furnace heats crude oil to ~360°C, while the vacuum furnace elevates temperatures to 380–420°C.
- Energy Consumption: Burners account for 20–30% of a refinery’s total energy usage, making their efficiency critical to operational costs.
- Temperature Control: Fractionation accuracy is highly sensitive to temperature fluctuations, necessitating stable, uniform heat output from burners.
A burner’s performance directly impacts a refinery’s profitability and environmental compliance.
II. Burners: The Core of Efficient Furnace Operation
1. Commanders of Thermal Efficiency
Burner design dictates fuel utilization efficiency:
- Complete Combustion: Advanced burners optimize air-fuel ratios and fuel atomization to ensure full combustion, minimizing unburned hydrocarbon emissions and maximizing heat release.
- Low Excess Air Ratio: Precise control of air-to-fuel ratios reduces heat loss via flue gas, boosting thermal efficiency (saving 5–10% in fuel costs).
- Heat Distribution: Burner layout and flame geometry ensure uniform heat distribution across furnace tubes, preventing localized overheating or cold spots.
2. Guardians of Environmental Compliance
Modern refineries face stringent limits on NOx, SOx, and particulate emissions:
- Low-NOx Technology: Staged combustion, flue gas recirculation (FGR), or premixed combustion reduce NOx emissions to below 50 mg/Nm³.
- Fuel Flexibility: Burners must adapt to diverse fuels (e.g., high-sulfur fuel oil vs. clean natural gas) while integrating desulfurization and dust-removal systems.
3. Frontline Defenders of Safety
Burner reliability is vital for preventing operational hazards:
- Anti-Flashback & Explosion Prevention: Pressure monitoring, flame detection, and emergency shutdown systems mitigate risks of fuel leaks or explosions.
- Corrosion & Coking Resistance: High-temperature-resistant materials and anti-coking designs combat degradation from sulfur or heavy fuels.
III. Burner Innovations and Challenges
As refineries transition toward smart, low-carbon operations, burner technology continues to evolve:
- Smart Control: IoT sensors and AI algorithms enable real-time monitoring of flame conditions, temperature, and emissions, allowing adaptive combustion optimization.
- Hydrogen Compatibility: Next-gen burners support hydrogen blending to reduce carbon footprints.
- Modular Design: Simplified maintenance and rapid component replacement minimize downtime.
IV. Burner Maintenance: Balancing Efficiency and Risk
Even cutting-edge burners require disciplined upkeep:
- Regular Cleaning: Remove carbon deposits and furnace coking to maintain efficiency and flame stability.
- Component Inspections: Inspect refractory materials, nozzles, and seals to prevent leaks or failures.
- Energy Audits: Thermal imaging and flue gas analysis identify hidden inefficiencies.
Though often overlooked, burners are the unsung heroes behind the performance of atmospheric and vacuum distillation furnaces. From cost savings and emissions reduction to safety and digitalization, every burner innovation propels the refining industry toward higher standards. As energy systems evolve, burners will remain pivotal in driving the sector’s sustainable transformation.For refineries, investing in burner upgrades is not just a technical decision—it’s a strategic imperative, directly shaping competitiveness and sustainability.